一台台工业机器人灵活地转动着机械臂,娴熟的完成着各项任务;一辆辆AGV小车在工房内来回穿梭,精准有序地将物料送达到位……这是国内首条应力释放罩制造黑灯生产线,工房内没有一人,只有机器在忙碌中有条不紊,随着真料经过一个个关卡,顺利完成各项生产任务,并达到144小时稳定运行,控制室里传出一阵阵欢呼声!历经两年艰苦卓绝的努力,经历三次技术迭代,经过项目团队超前谋划,紧前推进,特别是在四季度,为了加快进度保障生产线尽快通过各项评审并投入使用,惠安公司团结骨干人员,全力推进生产线试车的各项工作,提前迎来了应力释放罩制造黑灯生产线真料试车成功的喜讯。
应力释放罩的生产是惠安公司某重点产品生产的工艺窄口,不仅手工作业多,劳动强度大,还需要频繁的吊装作业,危险系数较高,而且工艺周期比较长。应力释放罩制造黑灯生产线的建设不仅将产线投用后单班作业人员由9人减至无人,还将日产能提高了3倍。以打造高科技、高效能、高质量生产线的探索与实践,点亮了引领惠安发展新质生产力的明灯。
由于应力释放罩制造属于涉火作业,因此惠安公司将每个环节的安全生产因素考虑在前,并将安全生产贯穿于应力释放罩制造黑灯生产线建设的全流程。该项目团队经过反复研讨,对生产过程设置了多重安全防护。一方面他们在工房的每个通道口设置了光栅,并将其与工房内的自动化设备进行联锁,当检测到人员进入后,设备会自动停机自锁,同时控制室也会接收到警报,实现了作业过程的无人化。另一方面,他们在重点部位安装了高清视觉识别系统,产品自动识别拍照,操作人员在控制室通过参数调整对焦定位后,下达指令进行精准操作。据悉,该视觉识别系统误差可控制在2mm内,这种精度是人工操作远远达不到的,一旦超出指标,系统会立刻报警,并停止生产,有效保障了安全生产的精准管控,提升了安全本质化程度。
由于生产线上所用的大部分设备都是非标加工设备,为了能让机器人操作的适配性和流畅性更强,他们对机械手部分进行了优化升级,加入了异常问题处置流程,机器人自动匹配和抓取工装进行预装配,通过力矩传感器的实时检测,确保了工装装配的一致性,有效提高了应力释放罩的生产质量,产品的良品率也由开始的70%提升到98%,目前各项指标还在进一步优化中。
除此之外,他们还对AGV小车进行了多次改良升级,一方面不断优化AGV小车与远程控制的适配度,不断提升运行地图的精度;另一方面将原有的轮子更换为万向轮,并添加了升降设备,使得AGV小车不仅功能更多,远程控制也更加精准。
应力释放罩制造黑灯生产线真料试车成功,标志着惠安公司向着建设现代化工企业的目标又迈了一大步。新质生产力是推动企业高质量发展的内在要求和重要着力点,惠安公司将坚持推进“人机黑”专项工作,持续抓好“黑灯工厂”建设,加快公司数智化转型发展,在发展新质生产力的道路上稳行至远。
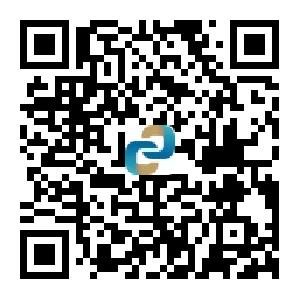